Spectrum Aeromed - medical interiors and equipment for fixed and rotor wing aircraft
Spectrum Aeromed - medical interiors and equipment for fixed and rotor wing aircraft
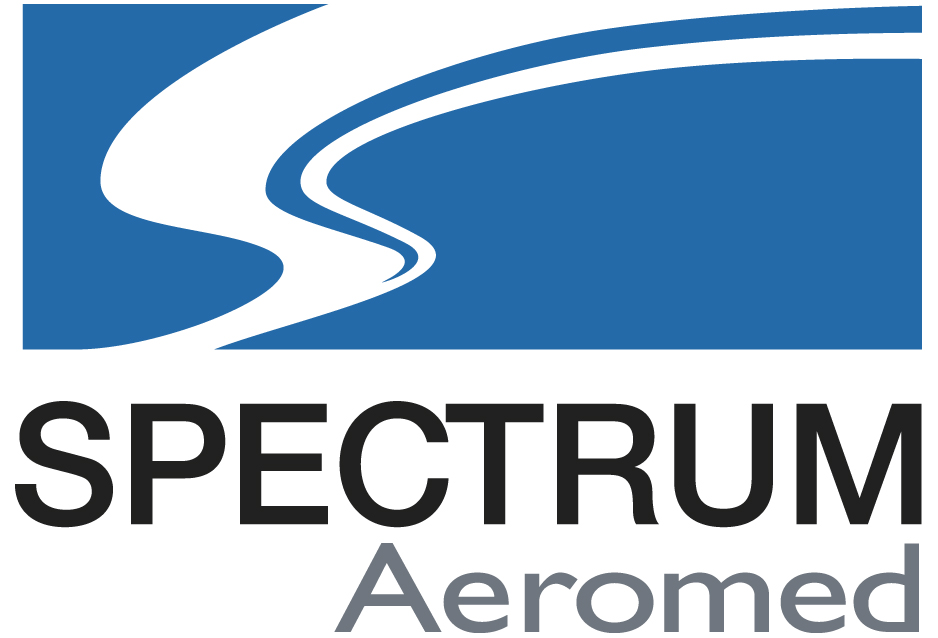
General company/production description
1. Please describe the product/service your company provides?Spectrum Aeromed designs and manufactures medical interiors and equipment for all kinds of fixed and rotor wing aircraft. The company has built a global reputation for customized interior solutions ranging from “quick change” technology that enables aircraft to be used for air ambulance or transport/charter purposes, to complete turnkey solutions for a fully dedicated medical interior. The company combines its engineering ability, technical expertise, and customer service commitment to create unique solutions to meet customer requirements.
2. What is unique about your company or product/service?

3. How does your company impact a specific industry?
Spectrum Aeromed’s headquarters are located within the renovated former terminal building at Fargo’s Hector International Airport, which provides multiple resources for a growing international business. First, the strategic location provides customers with easy access for on-site consultations. Second, the engineering and business talent being produced by several area universities has provided the company with many internships and several long-term employees. Lastly, partnering with neighboring Fargo Jet Center on the completion and delivery of several EMS mission installations into fixed wing aircraft has been a growing trend for the two companies. Spectrum Aeromed has excellent relationships with other aircraft completion centers as well as OEM’s worldwide, which ensures customers a quality turnkey solution.
Company history
1. When was the company started and who founded it?
Spectrum Aeromed began in Fargo, ND in 1991 by an air ambulance pilot and an aerospace Engineer, with the motivation to improve service quality of air ambulance services. The business moved to the small town of Wheaton, MN, then back to Fargo in 2008 where it is still headquartered with a 17,000-square-foot manufacturing facility.
2. When have there been major changes to product line or expansions?
Spectrum Aeromed invented the industry-recognized Seat Rail Adapter which allows any aircraft to be converted from standard configuration to air ambulance configuration in 30 minutes or less. In 1996, the 2800 Series module was certified and provided an extremely versatile solution which was lightweight and compact yet had critical care capabilities for larger aircraft. In 1999, a smaller stretcher was designed with tapered corners and a shorter module base, which still contained all the components for critical care transport in compact form for aircraft with limited floor space.
In more recent years, Spectrum Aeromed has expertise in carbon fiber lightweight designs for customers that require heavy duty capabilities. Spectrum Aeromed’s specialty equipment includes manual and electric patient loading systems, custom medical equipment mounts, cabinets, equipment tables, an incubator transport system for caring for infants, IV poles and oxygen boxes. Unique to Spectrum, the exclusively designed Medwall, Moveable Overhead and Stretcher Bridge were made for the direct mount of auxiliary medical equipment to provide easy access and flexibility for medical crews.
The Spectrum Aeromed team always works closely with air medical and patient transport crews to offer customized solutions that fit their needs. Over time, the company has seen a significant increase in highly customized projects requested by customers. This resulted in a business need for the company to develop a new standardized patient transport unit (PTU) module. The main objectives were to reduce customization, reduce parts, create a shorter lead time, and therefore offer customers a lighter weight and more aesthetically pleasing product. In 2021, Spectrum Aeromed announced its next generation patient transport unit, the Infinity Series 5000X. This new product gave Spectrum Aeromed the opportunity to differentiate from the competition by offering a more user-friendly module for medical crews and installers, which can be used across multiple aircraft installations. The 5000X offers an improved patient and installer experience with more clearance, easier maintenance access, reduced weight, and improved aesthetics. The modular, fully self-contained system has a smaller footprint and is one of the first products in the industry that was designed with and for flight nurses and medical teams.
3. What is significant/interesting about the history?
Spectrum understands the needs of its customers, not only from its years of experience, but also because its staff has a remarkable amount of operational experience in the aviation industry. On its management team alone, Spectrum has seven pilots and three airframe-and-powerplant mechanics, so it’s safe to say that the company has considerable insight into the unique requirements of aircraft equipment. That insight coupled with a team of talented engineers and efficient production staff has resulted in a line of quality products that are in service around the globe.
4. Who are current owners? Are you a corporation?
In 2019, the private investment group, Heartland Equity Partners partnered with the leadership team of Spectrum Aeromed to acquire the company. This investment set the stage for further advancements in new product design and innovation.
Customers
1. Who are your customers?Spectrum Aeromed’s air medical equipment is used by all segments of the aviation industry across the globe, including air charter services, private/VIP operators, royal families, emergency medical services (EMS) and search and rescue (SAR) operations, hospitals, corporations, as well as domestic and international military and government entities.
2. Where are they located?
Worldwide
3. Who should prospects contact at your company?
Depending on the location of the customer, sales representatives are assigned to territories which can be found here: https://spectrum-aeromed.com/sales-representatives/. Alternatively, contact Aeromed@Spectrum-Aeromed.com for assistance.
Current stats
1. How many people work at your company today?The company currently employs 32 people, with two remote sales offices located in Knoxville, TN and Friedberg, Germany.
2. Current certifications? (ISO, etc)
Assuring consistent processes and continually looking for new ways to advance its products and its industry is core to Spectrum Aeromed’s quality assurance standards and methodology. The company operates with lean manufacturing principles applied in every process and department within the company and has successfully completed all requirements for AS9100 Rev D certification. AS9100 is an aerospace industry standard on quality control and continuous improvement. Spectrum also maintains a U.S. Federal Aviation Administration (FAA) certificated repair station and employs an FAA-qualified DMIR (designated manufacturing inspection representative) and a qualified DER (designated engineering representative).
Spectrum Aeromed currently holds more than 90 Supplemental Type Certificates (STCs) covering around 450 models of aircraft, they work with the Federal Aviation Administration (FAA), European Aviation Safety Administration, (EASA), Canadian, and other international certification bodies to complete the appropriate approval process. The biggest barrier in the industry is certification or not having the STC to put equipment into an aircraft. There is significant engineering effort up-front to develop an STC, as well as a huge time factor. If Spectrum Aeromed does not have the approval of a specific STC, it makes it much more difficult to sell products if a direct competitor already has the STC approval. If both the customer and Spectrum Aeromed do not have an STC for an aircraft, Spectrum will work closely with the customer to obtain the necessary approvals and paperwork.

Due to COVID-19, there has been an increased request for isolation units. Spectrum Aeromed partnered with Isovac to support that demand and offer a safe solution for transporting infected patients amid the global pandemic. Spectrum Aeromed became a distributor of Isovac Products’ Containment and Protection System Utilizing Life Support (CAPSULS™) Patient Isolation Units (PIU’s), which integrate with Spectrum Aeromed’s equipment. (Caption: the standard patient module with medical wall and the ISOVAC patient isolation unit.)
Future
1. What are the future goals for the company?For much of the company’s history, the bulk of its business came from fixed-wing operators, but in recent years Spectrum has seen a marked increase in the number of interiors it has provided to the helicopter industry. That uptick is primarily owing to the growing trend of operators looking to get the most out of their helicopter investment by ensuring multi-mission capabilities. The company plans to continue to grow in the helicopter industry as well as fixed wing.